
“Un processus innovant”
PROCESSUS DE FORGEAGE COMPARÉ
Processus d’extrusion conventionnel
1| FONTE
- Four de fusion
- Dégazage
- Filtre
2| Coulée continue à refroidissement immédiat (DC casting)
3| Controle par ultrasons
4| Homogénéisation
5| EXTRUSION
- Scalpage
- Préchauffage
- Extrusion
- Pression
6| Straighten & Cut
7| FORGEAGE
Processus Forgeage liquide
1| FONTE
Four de fusion
Dégazage
Filtre
2| LIQUID FORGING
« Une technique unique de coulée d’alliages légers qui consiste à appliquer une très forte pression sur la matière à l’état liquide lors de la phase de solidification ».

Qualité, Polyvalence, Compétitivité!
L’écoulement complet de l’air contenu dans le moule est assuré par l’entrée lente du métal et par les cavités crées à cet effet.
Le compactage du métal durant la solidification permet la récupération de la forme désirée considérant le passage de l’état liquide à l’état solide.
La densité du produit est supérieure à celle obtenue avec n’importe quel type de processus de fonte traditionnelle (par gravité ou moulage métallique) et équivalente à celle obtenue avec le forgeage.
Le cycle de production, complètement automatique, est garenti grâce à des moyens techniques mise en place dans la topologie de la voiture.
Temps du cycle bien inférieur à celui du coulage sous-pression (rapport 1:2,5)
Tempo ciclo molto inferiore allo Squeeze Casting (rapporto 1:2,5)
QUALITÉ
DES ÉCONOMIES
• Intégrité de la structure.
• Absence de porosité.
• Plus haute tolérances dimensionnelles qu’avec la forge à chaud.
• Possibilité d’effectuer des traitements thermiques.
• Excellente micro-structure grâce à la solidification rapide suite au refroidissement forcé du moule.
• Adapté à tout type d’alliage léger y compris le magnésium (6082, 7075, 2014,0 A356, AlSi4.5, • AlSi9, Magsimal, Silafont…).
• Possibilité de produire des pièces avec embouts.
• Possibilité d’obtenir des pièces à géométrie complexe.
• Possibilité de produire des pièces allant de 40g à 10 kg.
• AUCUN DÉCHET!
• La quantité exacte du métal sert à la création de la pièce.
• Possibilité de créer des moules multiformes avec une réduction considérable du temps d’élaboration.
• Possibilité d’obtenir des formes diverses avec le même moule.
• Coût de production situé entre celui du moulage en coquille et celui du moulage métallique.
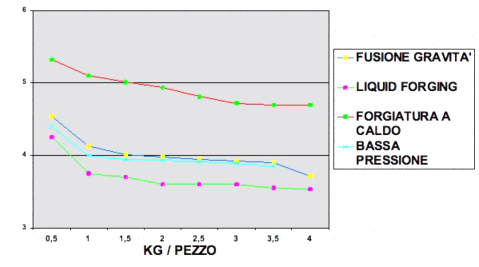
Le coût du forgeage liquide est inférieur à celui de la fusion par gravité, offrant en plus de meilleures caractéristiques qualitatives et mécaniques et une plus grande productivité.
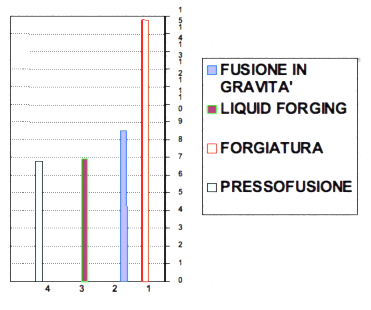
L’étude comparée montre le coût en Euros de la réalisation spécifique faite pour Volvo dans les diverses technologies.
Il convient de garder à l’esprit les coûts supplémentaires pour le moulage métallique,la fusion par gravité et la fusion à faible pression dûs à l’imprégnation à 100%, avec un écart allant de 6 à 20%.
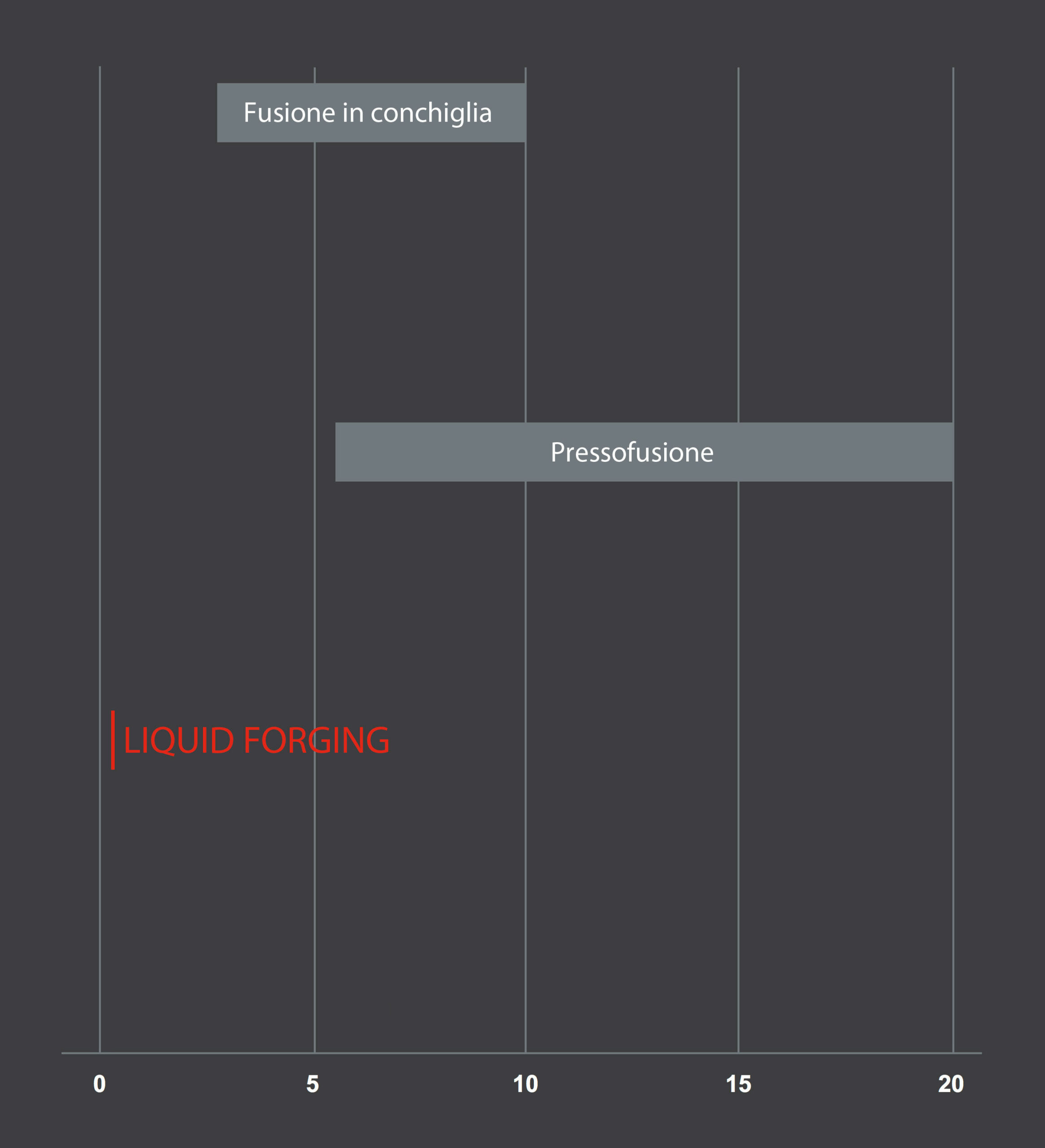
Pourcentage de porosité dans les différentes technologies.
ANALYSES
Les images radioscopiques illustrent la compacité du convertisseur de couple Volvo, on note l’absence de porosité, de microporosité, soufflement, fissure et cristallisation.(Ces caractéristiques sont communes à l’ensemble de la production).
EXAMEN AU MICROSCOPE
La microstructure correspondant à la superficie de la pièce apparaît très fine, sous l’effet du refroidissement extrêmement rapide du liquide.
La microstructure de la solidification eutectique interdendritique se trouve finement modifiée.
Le coeur de la structure a un haut dendritisme, avec une valeur moyenne de disance interdendritique d’environ 18 µm, indicateur de refroidissement rapide.
PROPRIETES MECANIQUES
La dureté du matériel est égale à 64,5 ÷ 67,5 HBW5/250, cohérente avec le non-traitement thermique de l’alliage. 3 prélèvements cylindriques ont été faits à partir de la pièce (L0=5xdiametro), soumis à une épreuve de traction selon le standard de la maison.
Le matériel est caractérisé par une valeur d’allongement comparable avec celle prévue par l’alliage même fondu à l’état semi-solide (thixoforage), selon tab. 53231. En outre 5 éprouvettes de résilience Charpy sans entaille ont été réalisées à partir de la pièce ; l’essai (effectué selon tab. 50130) a produit des valeurs égales à KC=43 ÷ 52 J/cm2 , élevées pour une pièce en alliage d’aluminium.
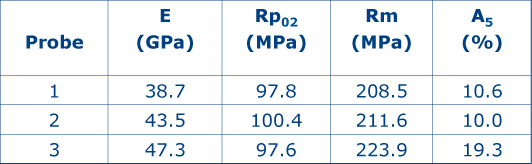
PATENT
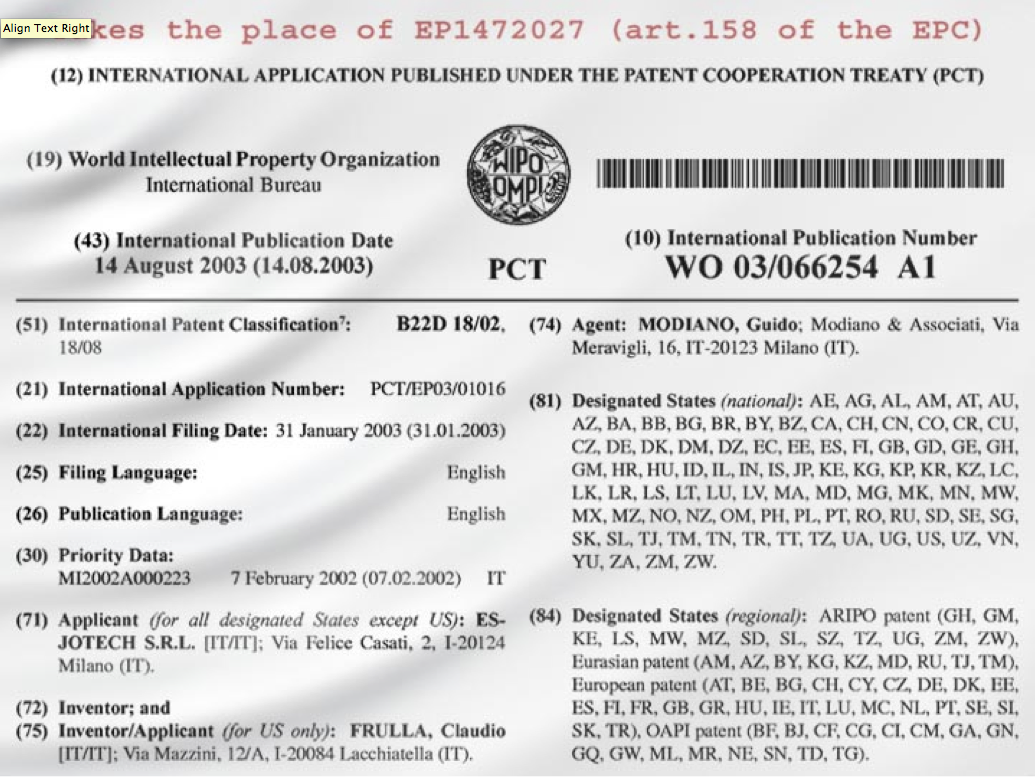