Géométrie TOECAP
More
+ THIN
Avec l’utilisation de la processus d’optimisation de la topologie et de la forme, les zones qui ne contribuent pas à la résistance structurelle sont identifiées.
More
+ LIGHT
Conformément à la forme requise, le matériel est distribué de manière à répondre aux contraintes et objectifs spécifiques requis.
More
+ RESISTANT
La nouvelle géométrie du TOECAP est bien dans les limites prescrites et il n’y a aucun risque de casse.
More
+ STRENGHT
Les tensions et la résistance aux contraintes sont mieux réparties qu’auparavant.
Cartographie des déformations plastiques de la section
Dans le Virtual Crash Test, la déformation plastique n’est que superficielle. Cartographie des critères de force de Von Mises.
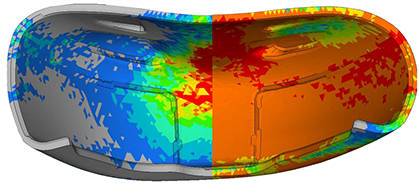
Une technique unique de coulée d’alliages légers
Application d’une très haute pression sur le matériau à l’état liquide lors de la phase de solidification.
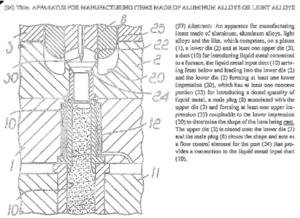
Perte de poids
Avec un poids moyen inférieur à 8 gr c’est le meilleur compromis entre poids et performance.
– 8 gr (-14,3 %)
Notre technologie nous permet d’utiliser du matériel uniquement là où il est nécessaire, nous évitons des coûts de matériel inutiles et réduisons le poids.
Notre embout le plus léger pèse 60 grammes et le plus lourd seulement 68 grammes.
Nous produisons toutes nos pointes en interne et les pesons dès qu’elles sont produites. Seules les pointes avec le bon poids continuent dans les processus ultérieurs car le poids est l’une des garanties de la qualité de la pointe.
Nous garantissons le poids avec une tolérance de +/- 3,5 grammes.
Avec nous, vous êtes plus compétitif
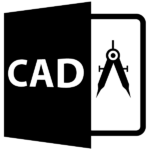
Fais le maintenant
Nous préférons l’obtenir tout de suite et ne pas perdre de temps et de ressources avec de nombreux tests pratiques. C’est pourquoi nous concevons les pointes avec CAD et les vérifions avec la technologie FEM avant de construire le moule. Nous simulons la résistance de la pointe et si nécessaire nous la modifions pour avoir la performance idéale.
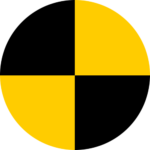
Nos moules
Nous construisons les moules uniquement avec de l’acier de haute qualité et les testons directement en production pour être sûrs de la capacité de production. Une fois le lot de production terminé, nous vérifions tous les moules, les nettoyons et, si nécessaire, les révisons avec notre personnel spécialisé.
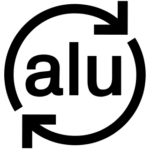
Alliage d’aluminium primaire
Nous produisons en interne l’alliage d’aluminium uniquement avec de l’aluminium primaire. Nous analysons chimiquement chaque lot d’alliage d’aluminium produit dans notre laboratoire. Bien sûr, nous conservons les données d’analyse pendant de nombreuses années.
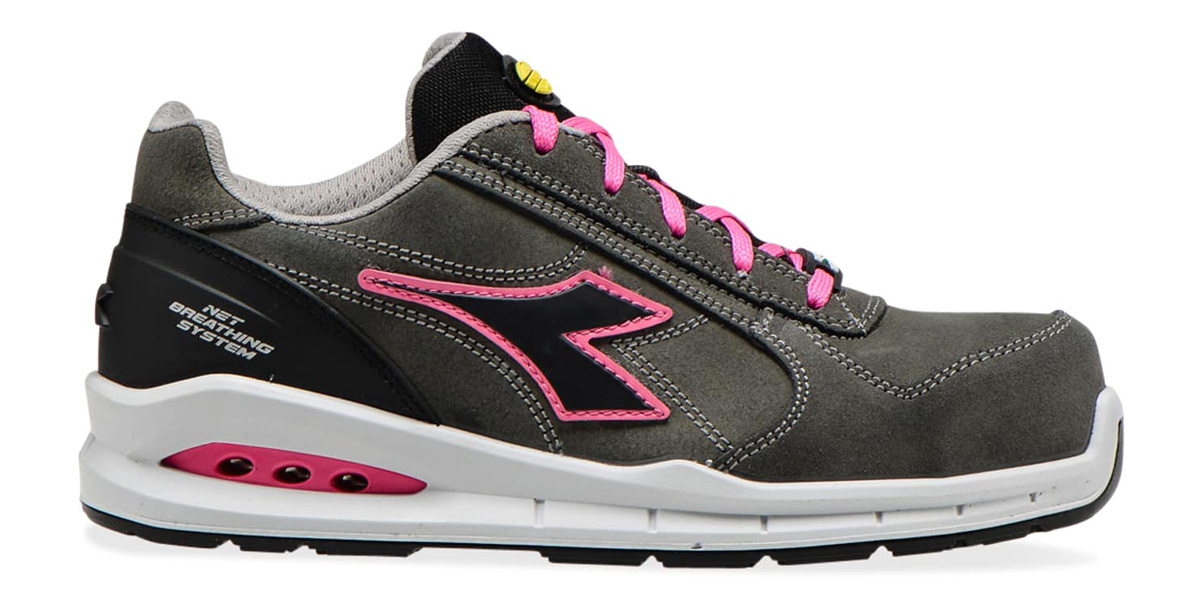
Nous sommes les seuls à produire même des petites pointures, même les femmes peuvent avoir des chaussures sûres et légères, à porter même au bureau. Nos embouts sont 2 fois plus légers que l’acier et moins encombrants que le plastique, mais sont tout aussi robustes.
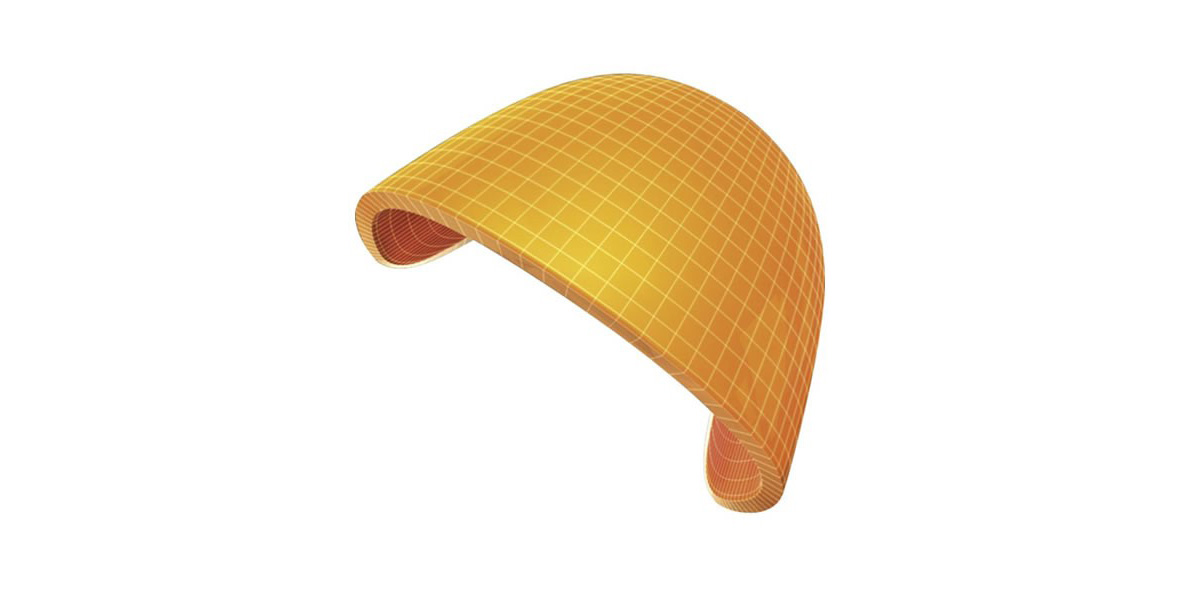
Nous avons 4 types de férules et des tailles de 5 à 12, il vous est facile de choisir la bonne férule grâce à nos dessins et échantillons.
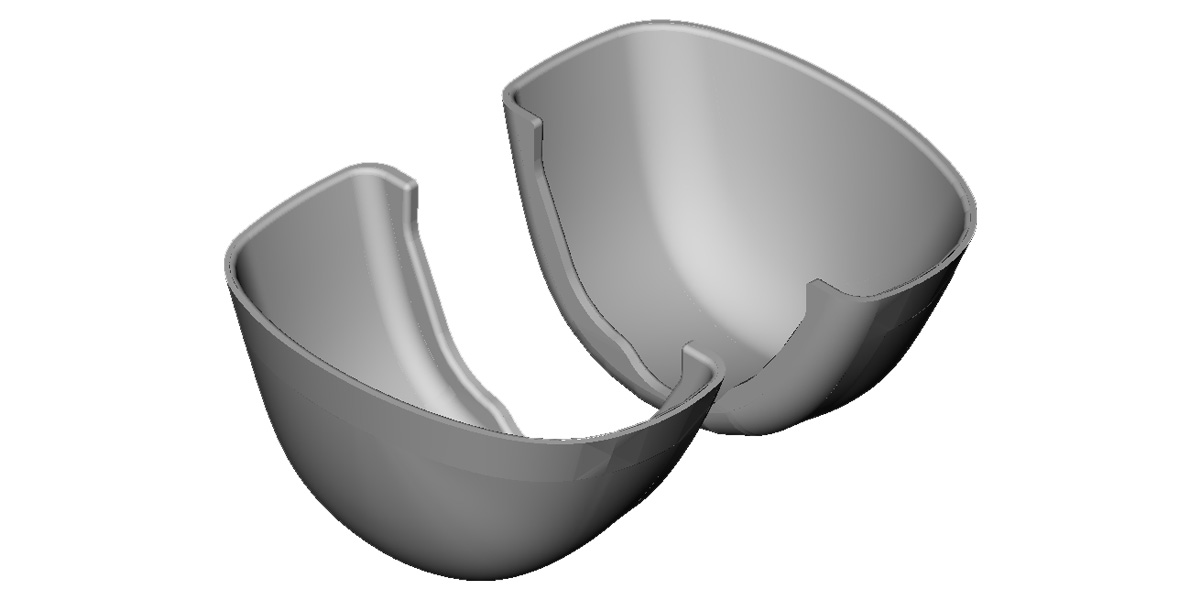